Industry
Essential sensors and switches for enhanced welding machine performance
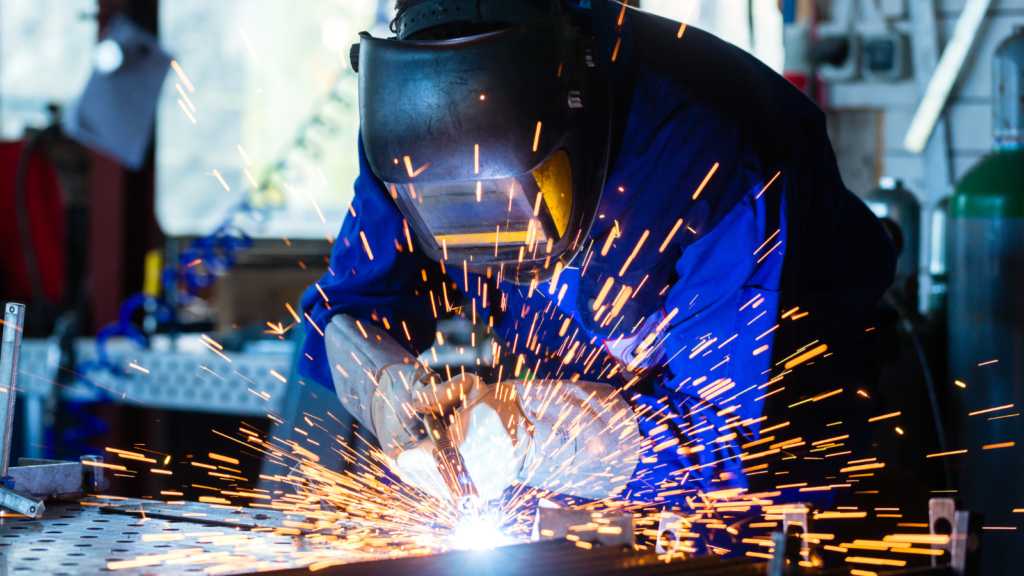
Welding machines are vital in industries such as construction, automotive, aerospace and manufacturing because they enable durable, high-strength bonds in structures, vehicles, equipment and more. They generate heat and power to fuse materials, usually metals or thermoplastics, by applying intense heat and sometimes pressure.
Welding machines use various sensors and switches to monitor and control aspects of the welding process, which includes:
- Improving weld quality by providing real-time data that helps maintain consistent welding parameters, ensuring the welding torch is positioned correctly and maintains the proper distance.
- Ensuring safety by monitoring the welding environment to ensure it remains within safe limits. They can trigger automatic shutdowns in case of unsafe conditions, minimising the risk of accidents.
- Enhancing efficiency and productivity by collecting data that can be used for quality analysis and predictive maintenance, as well as enabling automation and automated monitoring in large-scale or repetitive welding tasks.
Key sensing and switching components used in welding machines include those for monitoring temperature, tracking the precise position of the welding head, and detecting pressure levels to ensure consistent gas flow for weld integrity. Within Variohm Group, we provide many sensing and switching solutions for welding machinery, offering a streamlined procurement and supplier management process for customers. These include:
Encoders from Phoenix America
Encoders within the electric motor of the machine provide real-time positional feedback to control the precise movement of the welding torch, ensuring it follows the programmed path accurately. In applications that require intricate welding patterns or high repeatability standards, encoders allow the machine to follow complex paths and curves with precision. They are also used for tracking and controlling the speed and direction of the welding head or arm to achieve uniform welds.
Footswitches from Herga Technology
A footswitch enables the operator to start and stop the welding current with their foot, leaving their hands free to control the welding torch, hold materials in place or make adjustments during the weld. When activated, the machine remains on until the switch is flipped back to the off position. For added safety, some switches are designed with covers to prevent accidental activation.
Pressure switches from Herga Technology
Isolation gas is crucial for protecting the weld pool from atmospheric contamination, so ensuring its presence and flow at the correct pressure is vital. Pressure switches detect whether there is adequate gas pressure in the line before the welding arc is activated and during welding to ensure continuous gas flow. Any drop in pressure, which could be caused by a kinked hose or empty cylinder, triggers an alert or stops the process.
Temperature probes from Eurosensor
To control and monitor temperature in the cooling systems of laser welding machines, temperature probes provide real-time data to ensure safe and efficient operation. The process generates a significant amount of heat, and effective monitoring of the coolant fluid is required to prevent overheating, maintain stable operation and ensure weld quality. If the coolant temperature exceeds safe operating levels, the probe can trigger an alarm to protect the laser system from damage.
Temperature protectors from Limitor
Temperature switches are strategically placed on or near heat-sensitive parts of the welding machine and automatically trigger a response if any of the components reaches a temperature beyond the pre-set limits. This prevents further heat buildup, protects the equipment from damage and reduces the risk of fire.
Vacuum switches from Herga Technology
Fume extraction systems play a vital role in maintaining air quality and protecting workers from exposure to harmful fumes. Vacuum switches are a key component in the system, continuously monitoring the pressure level in the system and triggering an alert if the filter becomes blocked or full, allowing for proactive maintenance and ensuring safety.
Incorporating advanced sensing and switching solutions into welding machines is essential for ensuring safe, efficient and reliable operations. Collectively, the solutions offered by Variohm Group enhance equipment performance, extend machine lifespan, enhance safety and reduce downtime.
Please contact us to discuss how we can support your welding machinery projects.